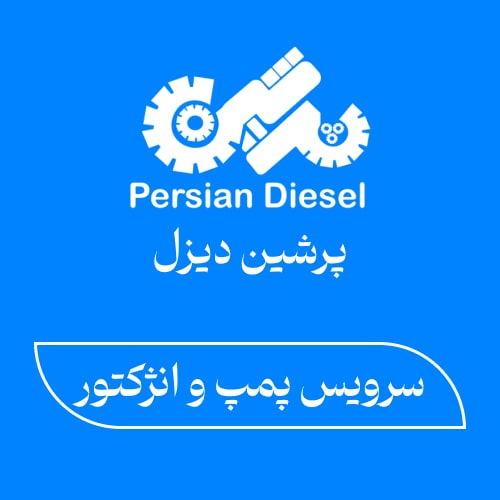
بررسی تاریخچه پمپ های دیزل
پمپ دیزل یکی از اجزای کلیدی در سیستمهای موتور دیزلی است که وظیفه تأمین و تزریق سوخت به داخل سیلندرهای موتور را دارد. تاریخچه پمپ دیزل به اختراع موتور دیزل و پیشرفتهای فناوری مرتبط با آن بازمیگردد. در ادامه به بررسی تاریخچه و توسعه این فناوری میپردازیم:
اختراع موتور دیزل
در سال 1892، رودولف دیزل، مهندس آلمانی، موتور دیزل را اختراع کرد. هدف او ایجاد موتوری بود که بهرهوری بالاتری نسبت به موتورهای بخار داشته باشد. این موتور با استفاده از فشردهسازی هوا و سوخت، کارایی بالایی ارائه داد.
اولین موتور دیزل، به جای استفاده از سیستمهای پیشرفته تزریق سوخت، از روشهای سادهتری برای تغذیه سوخت بهره میبرد.
پیدایش پمپ دیزل
در اوایل قرن بیستم، نیاز به کنترل دقیقتر تزریق سوخت به سیلندرها احساس شد. در این زمان، پمپهای مکانیکی دیزل توسعه یافتند. این پمپها، سوخت را با فشار بالا به انژکتورها ارسال میکردند تا به طور مستقیم در سیلندرها تزریق شود.
در دهه 1920 و 1930، شرکتهایی مانند بوش (Bosch) شروع به تولید سیستمهای تزریق سوخت پیشرفته کردند که شامل پمپهای دیزل دقیقتر بود.
توسعه فناوری پمپ دیزل
دهه 1950 تا 1980: با پیشرفت فناوری، پمپهای دیزل کارآمدتر و قابل اعتمادتر شدند. پمپهای مکانیکی با سیستمهای چندپیستونی توسعه یافتند که امکان تزریق یکنواخت و کنترل بهتر سوخت را فراهم میکرد.
دهه 1990: ظهور سیستمهای الکترونیکی مانند پمپ انژکتور الکترونیکی تحول بزرگی در این صنعت ایجاد کرد. این سیستمها قادر بودند تزریق سوخت را با دقت بالایی بر اساس شرایط موتور کنترل کنند.
پمپهای دیزل مدرن
در سالهای اخیر، فناوریهای جدیدی مانند سیستم ریل مشترک (Common Rail) معرفی شدهاند. در این سیستمها، پمپ دیزل سوخت را با فشار بسیار بالا به یک مخزن مشترک تزریق میکند و از آنجا، سوخت به انژکتورها توزیع میشود.
پمپهای دیزل مدرن به لطف استفاده از فناوریهای الکترونیکی و مواد پیشرفته، کارایی بالاتر، آلایندگی کمتر و عملکرد بهتری ارائه میدهند.
نسل های مختلف پمپ دیزل
تاریخچه نسلهای پمپ دیزل از توسعه اولیه موتورهای دیزلی آغاز شده و با پیشرفت فناوری در صنعت سوخترسانی تکامل یافته است. در اینجا به مراحل مهم و تحولات هر نسل از پمپهای دیزل اشاره میکنیم:
نسل اول: پمپهای مکانیکی خطی (In-Line Pumps)
در اوایل قرن بیستم و با اختراع موتور دیزل توسط رودولف دیزل، نیاز به سیستمهای دقیق سوخترسانی احساس شد.
ویژگیها:
دقت بالا: پمپ خطی به هر سیلندر مقدار مشخصی سوخت میرساند.
ساختار ساده: به دلیل طراحی مکانیکی ساده، نگهداری آن آسانتر است.
دوام: برای کار در شرایط سخت و طولانیمدت طراحی شده است.
چالشها:
کارایی پایین در تنظیم دقیق میزان سوخت.
نیاز به سرویس و تعمیرات مکرر.
بازدهی پایینتر: در مقایسه با سیستمهای جدیدتر مانند پمپهای انژکتوری مشترک (Common Rail)، بازدهی کمتری دارد.
آلودگی بیشتر: میزان کنترل دقیق سوخت کمتر از سیستمهای مدرن است و آلایندگی بیشتری ایجاد میکند
پمپهای مکانیکی خطی (In-Line Pumps) از نسل اول سیستمهای تزریق سوخت دیزلی هستند که در موتورهای دیزلی استفاده میشدند. این پمپها طراحی سادهای دارند و برای تامین دقیق سوخت مورد نیاز هر سیلندر به کار میروند. در زیر نحوه کارکرد این نوع پمپها توضیح داده شده است:
ساختار کلی پمپ خطی
بدنه اصلی: این پمپ دارای محفظهای است که چندین سیلندر (به تعداد سیلندرهای موتور) در آن قرار دارند.
پیستونهای تزریق: هر سیلندر دارای یک پیستون کوچک است که حرکت رفت و برگشتی انجام میدهد و سوخت را به داخل انژکتورها پمپ میکند.
میل بادامک: یک میل بادامک که توسط موتور به حرکت درمیآید، پیستونها را به حرکت درمیآورد.
سوپاپها و تنظیمکنندهها: سوپاپهایی برای کنترل ورود و خروج سوخت و یک مکانیزم تنظیمکننده برای تعیین مقدار و زمان تزریق سوخت وجود دارد.
مراحل عملکرد پمپ خطی
ورود سوخت به پمپ
سوخت از طریق یک پمپ اولیه (Low-Pressure Fuel Pump) به داخل پمپ خطی هدایت میشود.
در ورودی هر سیلندر، سوپاپی برای تنظیم ورود سوخت تعبیه شده است.
فشردهسازی سوخت
میل بادامک با چرخش خود پیستونها را در هر سیلندر به حرکت درمیآورد.
حرکت پیستون به سمت بالا باعث فشرده شدن سوخت در داخل محفظه میشود.
تزریق سوخت
هنگامی که فشار سوخت به حد معینی میرسد، سوپاپ خروجی باز شده و سوخت با فشار بالا به داخل انژکتور ارسال میشود.
انژکتور سوخت را به داخل محفظه احتراق موتور تزریق میکند.
تنظیم مقدار و زمان تزریق
زمانبندی و مقدار سوخت توسط مکانیزم تنظیمکننده پمپ انجام میشود.
این تنظیم بر اساس سرعت موتور و بار وارده تغییر میکند.
کاربردها
این پمپها در گذشته برای موتورهای دیزلی سنگین (کامیونها، اتوبوسها و ماشینآلات کشاورزی) بسیار رایج بودند، اما به دلیل ورود فناوریهای جدید، اکنون کمتر استفاده میشوند.
نسل دوم: پمپهای روتاری (Rotary Pumps)
این نسل در اواسط قرن بیستم توسعه یافت و با طراحی جمعوجورتر، مشکلات نسل قبلی را کاهش داد.
ویژگیها:
بهبود بازده انرژی: استفاده از مواد سبکتر و طراحیهای دقیقتر برای کاهش تلفات انرژی.
کاهش نشتی: بهینهسازی درزگیرها و آببندها (Seals) برای جلوگیری از نشتی سیال.
دوام بیشتر: استفاده از مواد مقاومتر در برابر سایش و خوردگی.
کاهش صدا و لرزش: طراحیهای جدید برای کاهش نویز و ارتعاش در حین عملکرد
مزایای نسل دوم پمپهای روتاری
راندمان بالاتر در مقایسه با نسلهای قبلی.
انعطافپذیری در جابجایی انواع سیالات با خواص مختلف.
عملکرد پایدارتر در فشارهای بالا.
نگهداری آسانتر به دلیل طراحیهای بهینه.
چالشها و محدودیتها:
هزینه اولیه بیشتر نسبت به نسلهای قدیمیتر.
نیاز به تعمیر و نگهداری دورهای برای اطمینان از عملکرد بهینه.
پمپهای روتاری (Rotary Pumps) از جمله پمپهای مکانیکی هستند که برای جابجایی مایعات یا گازها با استفاده از حرکت چرخشی طراحی شدهاند. این پمپها در نسل دوم خود بهبودهایی در طراحی و عملکرد داشتهاند که آنها را کارآمدتر و قابل اطمینانتر کرده است. در ادامه، نحوه کارکرد این پمپها توضیح داده میشود:
نحوه کارکرد پمپهای روتاری نسل دوم
اصول عملکرد:
پمپهای روتاری با ایجاد یک محفظه بسته بین یک روتور و محفظه اطراف آن کار میکنند.
روتور، که در داخل بدنه پمپ میچرخد، مایع یا گاز را به دام میاندازد و آن را از ناحیه ورودی (Suction) به ناحیه خروجی (Discharge) منتقل میکند.
انواع طراحی:
پمپهای روتاری نسل دوم میتوانند بر اساس نوع مکانیزم چرخشی در انواع مختلفی طراحی شوند:
پمپهای پرهای (Vane Pumps): پرههایی روی روتور قرار دارند که به صورت شعاعی حرکت میکنند و حجم محفظه را تغییر میدهند.
پمپهای چرخدندهای (Gear Pumps): از یک یا دو چرخدنده برای انتقال سیال استفاده میکنند.
پمپهای پیچی (Screw Pumps): از پیچهای مارپیچی برای حرکت سیال استفاده میکنند.
پمپهای لوبی (Lobe Pumps): دارای لوبهای دوار هستند که سیال را جابجا میکنند.
چرخه کاری:
مکش (Suction): زمانی که روتور میچرخد، فشار در ناحیه ورودی کاهش مییابد و سیال وارد محفظه میشود.
فشردهسازی (Compression): حرکت چرخشی روتور باعث کاهش حجم محفظه میشود، و سیال به سمت خروجی فشرده میشود.
تخلیه (Discharge): سیال تحت فشار از ناحیه خروجی خارج میشود.
کاربردها:
انتقال سیالات با گرانرویهای مختلف (روغن، سوخت، مواد شیمیایی و غیره).
استفاده در صنایع مختلف مانند نفت و گاز، غذایی، دارویی، و ماشینآلات سنگین.
این بهبودها و ویژگیها، نسل دوم پمپهای روتاری را به گزینهای مناسب برای کاربردهای صنعتی و تخصصی تبدیل کردهاند.
نسل سوم: سیستمهای انژکتوری مکانیکی (Mechanical Injectors)
در دهههای ۱۹۶۰ و ۱۹۷۰، پیشرفتهایی در دقت و کارایی پمپها ایجاد شد.
ویژگیها:
دقت بیشتر نسبت به سیستمهای کاربراتوری.
عملکرد پایدارتر در دماها و ارتفاعهای مختلف.
عدم نیاز به اجزای الکترونیکی پیچیده.
چالشها:
محدودیت در پاسخگویی به تغییرات سریع فشار.
تنظیم و تعمیر دشوار به دلیل پیچیدگی مکانیکی.
کارایی کمتر نسبت به سیستمهای انژکتوری الکترونیکی مدرن.
سیستمهای انژکتوری مکانیکی (Mechanical Fuel Injection Systems) نسل سوم از سیستمهای تزریق سوخت هستند که در دهههای میانی قرن بیستم توسعه یافتند. این سیستمها نقش مهمی در انتقال از سیستمهای کاربراتوری به سیستمهای تزریق سوخت دقیقتر و پیشرفتهتر داشتند. در ادامه به نحوه کارکرد این سیستمها میپردازیم:
تعریف کلی سیستمهای انژکتوری مکانیکی
سیستم انژکتوری مکانیکی با استفاده از پمپهای مکانیکی و اجزای دقیق مکانیکی، سوخت را به شکل مستقیم و دقیق به داخل سیلندرها یا ورودیهای هوا تزریق میکند. این سیستمها بدون نیاز به کنترلهای الکترونیکی کار میکنند و کاملاً وابسته به قطعات مکانیکی و هیدرولیکی هستند.
اجزای اصلی سیستم انژکتوری مکانیکی
پمپ سوخت مکانیکی (Fuel Injection Pump): پمپ مکانیکی وظیفه افزایش فشار سوخت و ارسال آن به انژکتورها را بر عهده دارد.
انژکتورهای مکانیکی: انژکتورها، سوخت را در فشار بالا به صورت ذرات ریز پاشش میکنند تا فرآیند احتراق بهینه انجام شود.
رگولاتور فشار: تنظیم فشار سوخت برای جلوگیری از پاشش بیش از حد یا ناکافی.
اهرمهای مکانیکی و بادامکها: این اجزا حرکت مکانیکی موتور را به حرکت دقیق پمپ و انژکتورها تبدیل میکنند.
نحوه کارکرد سیستم
تأمین سوخت: سوخت از باک خودرو توسط پمپ مکانیکی به فشار بالا رسانده میشود.
توزیع سوخت: پمپ انژکتور مکانیکی وظیفه توزیع سوخت را بر اساس زمانبندی احتراق و دور موتور دارد. این کار با کمک بادامکها و اهرمها انجام میشود.
پاشش سوخت: سوخت با فشار مناسب و در لحظه صحیح از طریق انژکتورها به داخل محفظه احتراق یا منیفولد هوا پاشیده میشود.
کنترل مقدار سوخت: مقدار سوخت بر اساس موقعیت پدال گاز و شرایط عملکرد موتور تنظیم میشود.
کاربردها
این سیستمها بیشتر در خودروهای قدیمی، هواپیماهای سبک و برخی تجهیزات صنعتی استفاده میشدند. از جمله کاربردهای معروف آنها میتوان به موتورهای مرسدس بنز (Bosch Mechanical Fuel Injection) و برخی خودروهای اسپرت کلاسیک اشاره کرد.
نسل چهارم: پمپهای انژکتوری الکترونیکی (Electronic Injection Pumps)
با ظهور فناوریهای الکترونیکی در دهه ۱۹۸۰، کنترل دقیقتری در سیستم سوخترسانی ایجاد شد.
ویژگیها:
کاهش مصرف سوخت: به دلیل مدیریت هوشمندانه سوخترسانی.
کاهش آلایندگی: با ترکیب سوخت و هوا به شکل بهینه.
افزایش قدرت موتور: به دلیل تزریق دقیق و احتراق کارآمدتر.
افزایش دوام قطعات: با کنترل دقیق فشار و زمان تزریق، سایش قطعات کاهش مییابد.
چالشها:
هزینه بالای تولید و تعمیر.
پیچیدگی سیستمها.
نسل چهارم پمپهای انژکتوری الکترونیکی (Electronic Injection Pumps) به طور خاص برای کنترل دقیق تزریق سوخت طراحی شدهاند و به عنوان یک پیشرفت چشمگیر در سیستمهای سوخترسانی خودروها شناخته میشوند. این پمپها از فناوریهای پیشرفتهای بهره میبرند که کارایی، بازده سوخت، و کاهش آلایندگی را بهبود میبخشند. در ادامه به نحوه کارکرد این سیستمها میپردازیم:
کنترل الکترونیکی:
این سیستمها از واحد کنترل الکترونیکی (ECU) برای مدیریت دقیق زمان و مقدار تزریق سوخت استفاده میکنند. ECU اطلاعات را از سنسورهای مختلف خودرو جمعآوری میکند، مانند:
سنسور دمای موتور
سنسور فشار هوا
سنسور موقعیت پدال گاز
سنسور اکسیژن (O2 Sensor)
این اطلاعات برای محاسبه دقیق نیاز سوخت در لحظه استفاده میشود.
مدیریت دقیق زمانبندی تزریق:
پمپهای انژکتوری الکترونیکی به کمک سولنوئیدها یا انژکتورهای الکترونیکی میتوانند زمان تزریق سوخت را با دقت بالا تنظیم کنند. این کار باعث میشود:
احتراق کاملتر انجام شود.
مصرف سوخت کاهش یابد.
آلایندگی کمتر تولید شود.
فشار بالای تزریق:
پمپهای انژکتوری الکترونیکی قادرند سوخت را با فشار بالا (بین 1800 تا 2500 بار یا بیشتر) به انژکتورها ارسال کنند. این فشار بالا موجب:
بهبود اتمیزاسیون سوخت (پخش شدن سوخت به ذرات ریزتر)
احتراق یکنواختتر در سیلندرها میشود.
انعطافپذیری در شرایط مختلف:
این سیستمها میتوانند بسته به نیاز موتور در شرایط مختلف (مانند بار زیاد یا سرعت بالا) مقدار و الگوی تزریق سوخت را تغییر دهند.
اجزای اصلی:
پمپ الکترونیکی: تأمین فشار سوخت.
سنسورها: برای دریافت دادههای عملیاتی.
انژکتورها: برای پاشش دقیق سوخت.
: ECU مغز سیستم برای مدیریت همهجانبه.
پمپهای انژکتوری الکترونیکی نسل چهارم یک پیشرفت حیاتی در سیستمهای سوخترسانی خودرو هستند که به کاهش مصرف سوخت، بهبود کارایی موتور، و کاهش آلایندگی کمک میکنند. این فناوری در خودروهای دیزلی و بنزینی پیشرفته امروزی به کار گرفته میشود.
نسل پنجم: سیستمهای ریل مشترک (Common Rail Systems)
این نسل از دهه ۱۹۹۰ توسعه یافت و تاکنون در موتورهای دیزلی مدرن استفاده میشود.
ویژگیها:
فشار تزریق بالاتر: فشار تزریق تا بیش از 2500 بار افزایش یافته است که موجب احتراق بهینهتر میشود.
کنترل دقیقتر تزریق: تزریق در چند مرحله انجام میشود تا لرزش و صدا کاهش یابد.
کاهش آلایندگی: با تزریق دقیقتر و احتراق کاملتر، میزان گازهای آلاینده کاهش مییابد.
افزایش بازدهی سوخت: مصرف سوخت کاهش یافته و عملکرد موتور بهینهتر شده است.
مزایا:
کاهش قابل توجه صدا و لرزش موتور.
افزایش عمر قطعات موتور به دلیل احتراق یکنواختتر.
کاهش مصرف سوخت و بهبود اقتصادی بودن.
کاهش آلایندگی محیط زیستی.
نسل پنجم سیستمهای ریل مشترک (Common Rail Systems)، که در خودروهای مدرن بهویژه دیزلی کاربرد دارند، بهبود قابلتوجهی در کارایی موتور، کاهش مصرف سوخت، و کاهش آلایندگی ارائه میدهند. در ادامه نحوه کارکرد این سیستم توضیح داده میشود:
اصل عملکرد سیستم ریل مشترک
ریل مشترک به یک مخزن فشار بالا اشاره دارد که وظیفه ذخیرهسازی و توزیع سوخت را برای انژکتورهای موتور بر عهده دارد.
این سیستم، سوخت را با فشار بسیار بالا (معمولاً بین 1000 تا 2500 بار) به انژکتورهای هر سیلندر ارسال میکند.
اجزای اصلی سیستم
پمپ فشار بالا: سوخت را از مخزن گرفته و با فشار بالا به ریل مشترک ارسال میکند.
ریل مشترک (Common Rail): وظیفه نگهداری و توزیع یکنواخت سوخت با فشار بالا را دارد.
انژکتورهای پیشرفته: سوخت را با کنترل دقیق در لحظه مناسب و با فشار مناسب به داخل سیلندر تزریق میکنند.
ECUواحد کنترل الکترونیکی): سیستم تزریق را بر اساس دادههایی مثل دمای موتور، بار موتور و دور موتور تنظیم میکند.
نحوه عملکرد
پمپاژ سوخت:
پمپ فشار بالا سوخت را از مخزن گرفته و آن را با فشار زیاد به ریل مشترک ارسال میکند.
نگهداری فشار در ریل مشترک:
فشار سوخت در ریل بهصورت یکنواخت و ثابت باقی میماند، حتی اگر موتور در سرعتهای مختلف کار کند.
تزریق سوخت:
ECUبا کمک سنسورها، لحظه و مقدار دقیق تزریق را برای هر انژکتور مشخص میکند.
این تزریق ممکن است به صورت پیشتزریق (Pilot Injection)، تزریق اصلی (Main Injection) یا تزریق پس از احتراق (Post Injection) انجام شود.
این سیستم به دلیل عملکرد پیشرفته و ویژگیهای آن، در خودروهای مدرن، بهویژه خودروهای دیزلی و حتی بعضی خودروهای بنزینی، به استاندارد تبدیل شده است.
نسل ششم: سیستمهای تزریق هوشمند و هیبریدی (Smart & Hybrid Systems)
در سالهای اخیر، فناوریهای جدید مانند سیستمهای تزریق هوشمند و هیبریدی برای بهینهسازی بیشتر مصرف سوخت و کاهش آلایندگی معرفی شدهاند.
ویژگیها:
ادغام فناوریهای الکترونیکی پیشرفته و هوش مصنوعی.
تزریق بسیار دقیق و زمانبندی بهینه.
هماهنگی با موتورهای هیبریدی و الکتریکی.
افزایش بهرهوری: بهینهسازی استفاده از مواد و انرژی.
کاهش هزینهها: کاهش هدررفت مواد و سوخت.
ارتقای کیفیت محصول: تولید قطعات دقیقتر و باکیفیتتر.
انعطافپذیری بالا: امکان تنظیمات پویا برای شرایط مختلف عملیاتی.
نسل ششم سیستمهای تزریق هوشمند و هیبریدی (Smart & Hybrid Systems) در صنایع مختلف، به ویژه در صنعت خودروسازی و تولید تجهیزات مدرن، ترکیبی از فناوریهای پیشرفته هوش مصنوعی، یادگیری ماشین و مهندسی مکانیک هستند. این سیستمها به منظور بهبود کارایی، کاهش مصرف انرژی و کاهش آلایندگی طراحی شدهاند. در ادامه به نحوه کارکرد این سیستمها پرداخته میشود:
تزریق هوشمند (Smart Injection Systems):
این سیستمها از سنسورها و الگوریتمهای پیشرفته برای بهینهسازی فرآیند تزریق استفاده میکنند.
ویژگیها و نحوه عملکرد:
کنترل دقیق فشار و دما: سنسورها به صورت لحظهای فشار و دمای محیط را اندازهگیری کرده و آن را با شرایط ایدهآل مقایسه میکنند.
مدیریت جریان مواد: میزان دقیق ماده مورد نیاز برای تزریق با کمک سیستمهای هوشمند محاسبه میشود تا از هدررفت مواد جلوگیری شود.
تصحیح خودکار خطاها: اگر خطا یا عدم تعادل در فرآیند تزریق رخ دهد، سیستم به طور خودکار تنظیمات لازم را انجام میدهد.
افزایش دقت: در تولید محصولات پیچیده مانند قطعات کوچک یا دارای جزئیات زیاد، این سیستمها دقت بسیار بالایی ارائه میدهند.
سیستمهای هیبریدی (Hybrid Systems):
این سیستمها از ترکیب دو یا چند منبع انرژی (مانند الکتریکی و مکانیکی) برای انجام وظایف استفاده میکنند.
ویژگیها و نحوه عملکرد:
استفاده ترکیبی از منابع انرژی:
در ماشینهای صنعتی، از انرژی الکتریکی برای کارکرد پایه و از انرژی مکانیکی یا هیدرولیکی برای عملیات سنگینتر استفاده میشود.
در خودروها، ترکیب موتورهای الکتریکی و احتراقی منجر به کاهش مصرف سوخت و افزایش راندمان میشود.
مدیریت هوشمند انرژی:
سیستمهای کنترلی با توجه به بار کاری، شرایط محیطی و نیاز عملیاتی، منبع انرژی مناسب را انتخاب میکنند.
برای مثال، در ترافیک شهری از موتور الکتریکی و در جادههای باز از موتور احتراقی بهره میگیرند.
بازیابی انرژی (Energy Regeneration):
در سیستمهای هیبریدی، انرژی اتلافی (مانند گرمای ترمز یا ارتعاشات) بازیابی و به چرخه مصرف بازمیگردد.
کاربردها:
صنعت خودروسازی: خودروهای هیبریدی و برقی.
صنعت قالبسازی: ماشینهای تزریق پلاستیک هوشمند.
تجهیزات پزشکی: تولید قطعات کوچک و دقیق.
الکترونیک: تولید بردهای مدار چاپی و قطعات ریز.
چالشها و آینده پمپ دیزل
با توجه به تأکید روزافزون بر کاهش آلایندگیهای زیستمحیطی، پمپهای دیزل نیز تحت فشار هستند تا بهبود یابند.
استفاده از سوختهای جایگزین مانند بیودیزل و توسعه موتورهای هیبریدی یا الکتریکی ممکن است در آینده جایگاه پمپهای دیزل را تغییر دهد.